Case Study 1: Door Assemblies
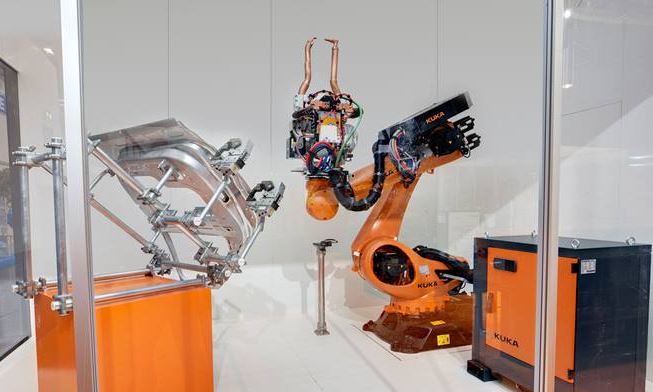
One major agricultural equipment manufacturer implemented robotic spot welding to improve the efficiency of their door assembly process. They aimed to achieve a cycle time of 5 minutes per part. However, with the help of a robotic controller kit, they were able to achieve a cycle time of 4.5 minutes per part - 10% faster than the initial requirement.
The robotic spot welder also achieved the manufacturing requirements. The spot welds were achieved without any cracks, and there was thorough fusion while maintaining an acceptable aesthetic quality.
The benefits for the manufacturer were numerous. By using a robotic controller kit, they were able to reduce the time spent on door assembly, improve the accuracy and consistency of spot welding, and minimize the risk of worker injury. Moreover, the manufacturer also saved money in the long run by eliminating the need for manual labor, reducing the risk of rework, and improving product quality.
Case Study 2: Shield Door Assemblies
Another major agricultural equipment manufacturer implemented robotic spot welding to improve the efficiency of their shield door assembly process. They aimed to achieve a cycle time of 3 minutes per part, and with the help of a robotic controller kit, they were able to achieve a cycle time of 2.5 minutes per part - 17% faster than the initial requirement.
The robotic spot welder achieved manufacturing requirements for the shield door assemblies. The spot welds were achieved without any cracks, and there was thorough fusion while maintaining an acceptable aesthetic quality.
The benefits for the manufacturer were again numerous. By using a robotic controller kit, they were able to reduce the time spent on shield door assembly, improve the accuracy and consistency of spot welding, and minimize the risk of worker injury. The manufacturer also saved money in the long run by eliminating the need for manual labor, reducing the risk of rework, and improving product quality.
Advantages of Robotic Spot Welding with a Welding Robotic Controller Kit
Robotic spot welding for agricultural equipment manufacturing offers numerous advantages:
1. Improved Efficiency: Robotic spot welding is faster and more consistent than manual welding, which improves efficiency and productivity.
2. Accuracy and Consistency: Robots can consistently apply the right amount of pressure to achieve spot welds with the same quality every time.
3. Improved Quality: Robotic welding eliminates the risk of errors, rework, and human error, which improves the quality of the final product.
4. Reduced Cost: Robotic welding reduces the need for manual labor, which reduces labor costs in the long run.
5. Improved Safety: Robotic welding eliminates the risk of injury for human workers.
Conclusion
Robotic spot welding with a welding robotic controller kit offers numerous advantages for agricultural equipment manufacturers. By implementing robotic spot welding, manufacturers can improve efficiency, accuracy, consistency, and quality while reducing costs and improving safety. These two case studies show that robotic spot welding is a valuable investment for agricultural equipment manufacturers looking to improve their welding process.