The manufacturing of plastic particles requires a high degree of precision and cleanliness to ensure the end product’s consistency and quality. One of the most critical steps in this process is material handling, wherein plastic particles are transported and sorted with minimal contamination.
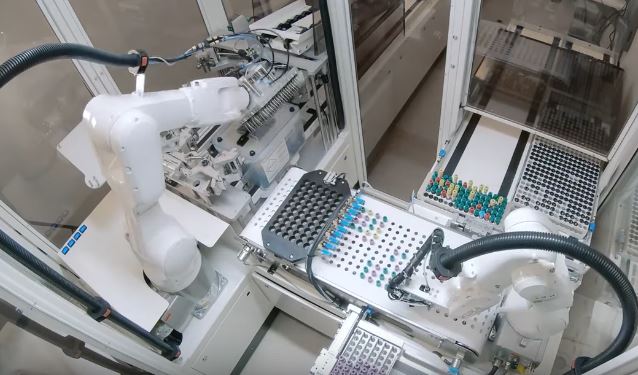
Infineon Technologies Austria AG, a leading producer of semiconductors and microelectronics, has found a reliable partner in KUKA’s cleanroom robots for the handling of silicon wafers. KUKA’s robots are sensitive, precise, and boast a cleanroom rating, making them ideal for the most demanding material handling requirements.
Cleanroom robots are designed to operate in controlled environments, such as semiconductor cleanrooms or facilities used for pharmaceutical manufacturing. They must adhere to strict standards for particle exclusion, avoid electrostatic discharge, and prevent the outgassing of material. KUKA’s LBR iiwa CR robots are capable of operating in Class 5 cleanrooms, with a particle count limit of 100,000 per cubic meter.
The LBR iiwa CR robot is sensitive enough to handle delicate materials without damaging them. Its unique design allows for contact sensing, which means it can detect when it comes into contact with an object, and adjust its movements accordingly. This feature is especially useful when handling brittle materials like silicon wafers, where even the slightest pressure can cause damage. As a result, KUKA’s cleanroom robots are a cost-effective solution as they minimize the need for additional equipment or manual labor.
Another advantage of KUKA’s robots is their flexibility. The LBR iiwa CR robot has seven joints, making it highly adaptable to various material handling tasks. Its programmable nature means it can be reconfigured to handle different materials with varying sizes, shapes, and weights. This is particularly useful in the plastic particle industry, where materials can come in various forms and sizes.
KUKA’s robots also have built-in safety features, making them safe to operate around humans. The robots have torque sensors that detect when they encounter resistance while moving, and they will stop or slow down to avoid injuries. This feature is especially crucial in environments where humans and robots work side by side.
By using KUKA’s cleanroom robots, Infineon Technologies Austria AG has minimized downtime, reduced errors, and increased productivity. The robots work around the clock, leading to 24/7 operations with minimal supervision. They are also more consistent than humans, ensuring that the final product meets the strict quality standards required.
In conclusion, KUKA’s LBR iiwa CR robots are a game-changer for the plastic particle industry. They are highly sensitive, adaptable, and safe to operate around humans. By implementing KUKA’s robots, manufacturers can streamline their operations, increase productivity, and reduce costs. KUKA is at the forefront of the material handling industry, and its cleanroom robots are setting new standards for performance and reliability.