Welding is a critical process in several industries, including aerospace, marine, automotive, and construction. Welding enables the joining of metals, which are essential in the manufacture of many products. However, welding requires a high level of accuracy, and even the smallest mistakes can lead to significant problems in the final product. One of the most challenging aspects of welding is maintaining a consistent seam while welding, which can lead to structural problems in the finished product. It is essential to have a reliable welding seam tracking system to ensure the success of the welding process.
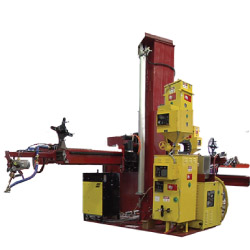
A welding seam tracking system is an automated system that uses advanced sensors to track the welding seam in real-time. This system precisely monitors the position of the welding seam and adjusts the welding torch to maintain a consistent distance from the seam. A welding seam tracking system can significantly improve the efficiency of the welding process and reduce the need for human intervention. Moreover, it ensures that the welding process is precise and accurate, creating high-quality products.
Gas Tungsten Arc Welding
Gas tungsten arc welding (GTAW) is a welding process that uses a non-consumable tungsten electrode to heat the metal. GTAW is also known as TIG welding, and it is commonly used on thin sheets of metal. GTAW is widely used in the aerospace industry, particularly for welding titanium alloys. Titanium alloys are difficult to weld due to their high thermal conductivity and low heat capacity. GTAW is an ideal welding technique for welding titanium alloys because it produces a high-quality weld and provides precise control over the heat input.
Welding Seam Tracking System
A welding seam tracking system is critical for achieving high-quality welds in titanium alloys using GTAW. The traditional method of welding titanium alloys involves manual tracking of the welding seam, which is time-consuming and requires a high level of skill. A vision-based welding seam tracking system provides a more efficient and precise way of tracking the welding seam.
The vision-based welding seam tracking system uses a high-resolution camera to capture real-time images of the welding seam. The camera is mounted on the welding torch, which provides a clear view of the welding seam. The system uses advanced image processing techniques to extract the features of the welding seam from the captured images. The system then uses these features to track the welding seam in real-time.
The tracking system adjusts the position of the welding torch based on the position of the welding seam, maintaining a consistent distance from the seam. This system ensures that the weld is regularly spaced along the welding seam, which is essential for maintaining the strength and integrity of the weld. Moreover, the vision-based welding seam tracking system reduces the need for human intervention, improving the efficiency of the welding process.
Advantages of a Welding Seam Tracking System
A welding seam tracking system is a valuable tool for achieving high-quality welds in titanium alloys using GTAW. The system provides several advantages over traditional manual tracking methods, including:
1. Improved Efficiency: The welding seam tracking system significantly reduces the need for human intervention, improving the efficiency of the welding process.
2. Precise Control: The system provides precise control over the welding torch's position, ensuring that the weld is regularly spaced along the welding seam.
3. Consistency: The welding seam tracking system ensures that the weld is consistently spaced along the welding seam, which is essential for maintaining the strength and integrity of the weld.
4. Quality: The system produces high-quality welds, ensuring that the final product meets the required specifications.
Conclusion
A vision-based welding seam tracking system is critical for achieving high-quality welds in titanium alloys using GTAW. The system provides precise control over the welding torch's position and ensures that the weld is consistently spaced along the welding seam. The system significantly improves the efficiency of the welding process and reduces the need for human intervention, improving the overall quality of the final product. A welding seam tracking system is an essential tool for any industry that requires high-quality welds in titanium alloys.