Robotic welding is becoming more and more popular as manufacturing processes become automated. With advancements in technology, robots are becoming more intelligent and capable of performing complex tasks. One of the most common welding methods for robots is TIG welding. However, a newer technology, ultrasonic welding, is becoming more prevalent for certain applications. In this article, we will compare the two methods to help you determine which is best for your production needs.
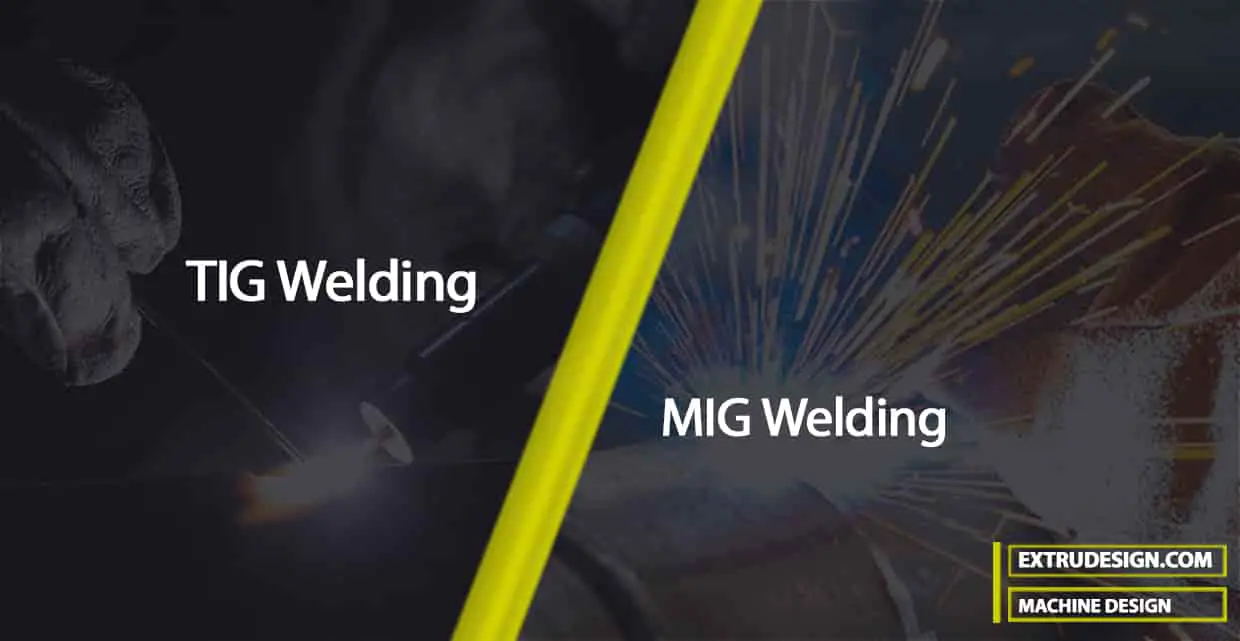
Firstly, let us explore the basic principles behind each type of welding. In TIG welding, a tungsten electrode is used to create an arc that melts the base metal and filler material, producing a permanent bond. The tungsten electrode remains unreactive throughout the process, ensuring that it does not contaminate the weld.
On the other hand, ultrasonic welding uses high-frequency vibrations to join metals. The two pieces of metal to be welded are pressed together with an ultrasonic vibration applied on the joint. The vibration creates heat which locally melts the metal at the joint. After the vibration stops, the melted metal cools and hardens, forming a lasting bond.
One of the most significant advantages of ultrasonic welding is that it does not require filler material. This makes it a more cost-effective option, as there is no need to stock a range of filler materials. Additionally, ultrasonic welding produces fewer fumes and requires less energy than other welding techniques. This makes it a more environmentally friendly choice.
Furthermore, ultrasonic welding produces less heat compared to TIG welding, which may generate less distortion in the metal. This means that ultrasonic welding could be a better option for welding thin materials, as it will produce less warping and buckling.
However, ultrasonic welding has its drawbacks too. For instance, it is not suitable for all materials. Ultrasonic welding is not effective for welding thicker materials, as it requires comparatively high-frequency vibrations to produce a bond. This means that the metal must have a sufficient degree of flexibility to vibrate at the required frequency.
Also, ultrasonic welding is not precise enough for highly complex joints. It is only useful for simple butt joints or lap joints, where the two metals can be held in alignment long enough for the heat to set.
By contrast, TIG welding is optimal for precision, multi-pass welds that require a high level of accuracy. TIG welding is excellent for welding complex structures with multiple layers of metal.
TIG welding also produces a more aesthetically pleasing weld. Because TIG welding uses a tungsten electrode, it produces a narrow arc that creates a neat, clean weld that is appealing to the eye. This makes it an outstanding choice for applications where aesthetics are a factor.
TIG welding has disadvantages too, however. Firstly, it requires constant operator attention, as the weld requires precise control of speed and heat output. This can make it a more laborious process, as opposed to ultrasonic welding which is automated.
Additionally, TIG welding is often costlier than other types of welding. Not only is it more time-consuming, but it requires a skilled operator, and the cost of the tungsten electrode and filler material can be substantial.
To sum up, when choosing between ultrasonic and TIG welding, it is crucial to consider the specific demands of your manufacturing process. Both methods have their benefits and drawbacks, and there is no one-size-fits-all solution. You need to weigh the factors that are most important for your business, such as cost, speed, precision, and material compatibility.
Shanghai Jiesheng robot, based in China, is at the forefront of welding system design and development. We offer a range of high-tech welding machinery that provides superior value to businesses, no matter how challenging their requirements. Our expert technicians are available to advise you on the best processes and tools for your needs to ensure you get optimal results every time.
In conclusion, choosing the right welding technology is crucial for a successful manufacturing operation. Both ultrasonic and TIG welding have their advantages, and it is vital to consider the specific needs of your business before deciding which method to use. By partnering with Shanghai Jiesheng robot, you can access the latest welding technologies and expert guidance to achieve optimal results for your business.