TIG welding is a high-precision welding technique that requires a steady hand and a trained eye. The process involves using a non-consumable tungsten electrode to heat the metal and create an arc, which melts the metal and forms a weld. The TIG welding process produces a clean, precise weld with minimal heat input, making it ideal for welding high-quality, thin materials such as aluminum, copper, and stainless steel.
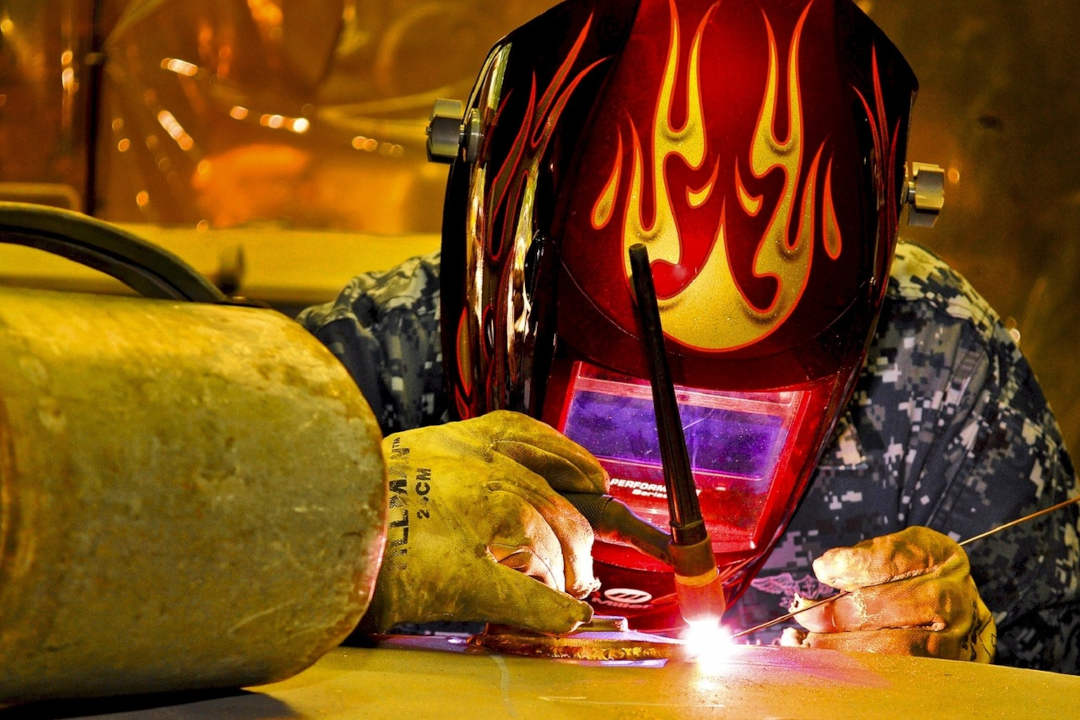
While TIG welding has always been a popular technique in the manufacturing industry, it wasn't always easy to automate due to the precision required. However, with the evolution of robotics technology, TIG welding robots have become increasingly popular in recent years. These robots offer a variety of benefits, including increased productivity, accuracy, safety, and cost savings.
One of the main benefits of TIG welding robots is increased productivity. These robots never tire and can work for long periods without breaks, leading to a more consistent and productive welding process. Robots also have the ability to work in hazardous or hard-to-reach areas, reducing the need for human workers to operate in dangerous conditions.
Another benefit of TIG welding robots is accuracy. As mentioned before, TIG welding requires a steady hand and a trained eye to produce a high-quality weld. However, with TIG welding robots, precision is built-in. These robots use sensors to ensure the correct welding parameters, leading to consistent output and higher-quality welds.
TIG welding robots also increase safety in the workplace. Welding is a hazardous activity, requiring protective equipment such as face shields, gloves, and flame-resistant clothing. However, with TIG welding robots, the process becomes entirely automated, reducing risks of human error and injury.
Finally, TIG welding robots can also offer cost savings in the long run. While the initial investment in a TIG welding robot can be high, their long-term efficiency and productivity often result in lower costs than hiring and training human workers.
In conclusion, TIG welding robots are becoming increasingly popular in the manufacturing industry due to their ability to increase productivity, accuracy, safety, and cost savings. With their ability to work in hazardous areas, adapt to different materials, and reduce the need for human workers, TIG welding robots are truly revolutionizing the welding process. If you're looking to increase your productivity and efficiency in the manufacturing process, a TIG welding robot may be the solution for you.